Bezoek | Mavic: op zoek naar een nieuw elan
Door Léo Kervran -
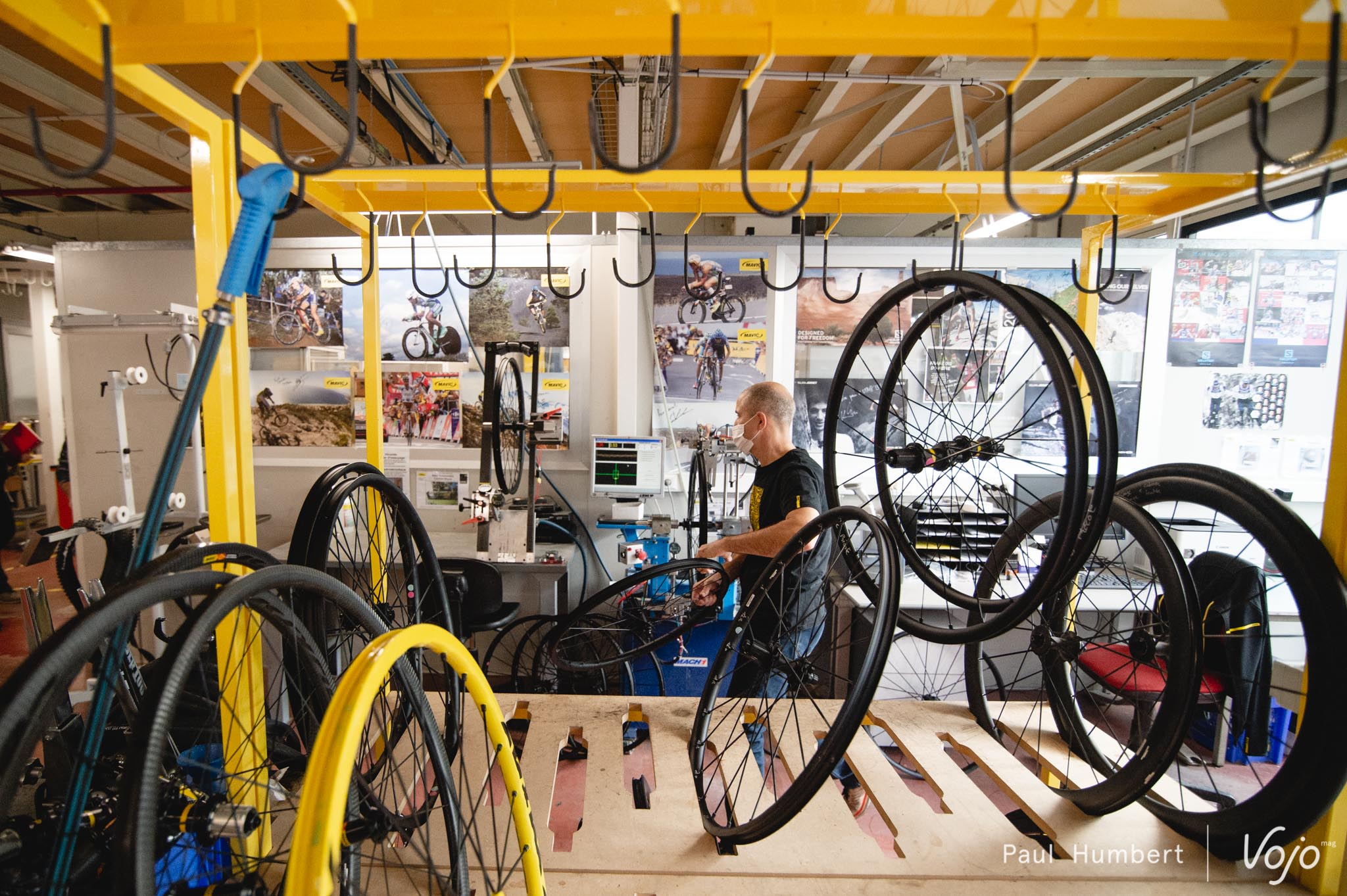
Mavic stond al langer op ons verlanglijstje om er ooit een keertje de fabriekspoort binnen te wandelen en hen met een bezoek te vereren. Het hoofdkantoor van het merk bevindt zich slechts enkele kilometers van de Franse poot van Vojo, wat het idee enkel maar deed groeien. Enkele weken geleden was het dan eindelijk zover, net op het moment dat de kleine productie-eenheid ter plaatse weer begon te draaien. Ons bezoek werd dan ook heel wat interactiever dan voorzien …
Moeten we Mavic nog voorstellen? Het merk ontstond in 1882 en was lange tijd een van de kroonjuwelen van de Franse fietsindustrie en alomtegenwoordig in de wielersport. Na enkele moeilijke jaren en een gerechtelijke reorganisatie, herrijst het merk anno 2021 eindelijk uit zijn assen en wil het zijn plaats binnen de groten in de industrie zo snel mogelijk terug opeisen.
Mavic heeft de reputatie regelmatig met vernieuwende producten uit te pakken, ook al waren niet alle ideeën uit het verleden altijd even succesvol: denk maar aan de eerste geanodiseerde velgen in 1975, het paraculaire Comète-wiel in 1985 (meer dan 10 jaar na de eerste prototypes), een elektrische aandrijving in 1992 en vervolgens in 1999 een draadloze aandrijving, een wiel-band-systeem in 2010, enz. In het mountainbiken moeten we teruggaan tot 1985 toen Mavic voor het eerst een MTB-velg uitbracht voor een sport die toen nog in zijn kinderschoenen stond.
In 1999 maakte Mavic naam met het Fore-concept: het merk slaagde erin om alleen door de eerste wand van de velg te boren om de spaak te bevestigen, waardoor de bovenwand intact blijft. In datzelfde jaar bracht deze innovatie het UST Tubeless-systeem voort, waardoor montages zonder binnenband populairder werden. Een paar jaar later reden de Crossmax SLR (XC) en de Deemax (DH) het merk naar de top van de wereldpodia, wat duizenden enthousiastelingen over de hele wereld over deze wielen deed dromen.
Rond 2010 ziet het er echter plots heel wat minder rooskleurig uit voor Mavic. Op technisch vlak heeft het merk te maken met betrouwbaarheidsproblemen en communicatie die niet aan de verwachtingen van zijn klanten voldoet, terwijl het op de achtergrond kampt met financiële moeilijkheden en een verwarring rond zijn eigenaar. Pas eind juli 2020 schijnt er na drie maanden onder gerechtelijk bewind weer wat licht aan het eind van de tunnel, na de overname door de Bourrelier-groep (ook eigenaar van de Karwei- en Gamma-winkels).
Vandaag telt Mavic 109 werknemers, wat iets minder is dan de helft van het personeel dat voor de overname door de Bourrelier-groep bij het bedrijf aan de slag was. Een belangrijke maar noodzakelijke inkrimping om het merk te laten herstellen en de harten van de klanten terug te winnen. “We functioneren voortaan zoals een middelgrote onderneming”, legt Michel Lethenet uit, de persverantwoordelijke en onze gids van de dag. Meer flexibiliteit en transparantie kan geen kwaad wanneer je technologische nieuwigheden, prestaties en betrouwbaarheid met elkaar wil verzoenen.
Michel stelt ons ook gerust over wat bij het merk onder de noemer ‘soft’ valt, zijnde de helmen, schoenen en kleding. Toen Bourrelier de overname aankondigde, ‘vergat’ men deze divisie, maar ze heeft wel degelijk nog een toekomst bij het merk en we zullen deze producten dan ook niet snel zien verdwijnen. We mogen zelfs de nodige veranderingen verwachten in het assortiment, omdat Mavic, net als bij de wielen, heeft aangekondigd het assortiment te vereenvoudigen. Merk ook op dat Mavic van plan is om de fabricage van deze producten naar de Europese Unie te repatriëren (sommige producten worden nog steeds in de Maghreb gemaakt), zoals al het geval is voor de wielen.
Om de expertise van Mavic beter te begrijpen, stelt het merk ons voor zelf een carbon wiel te fabriceren …
Je begrijpt dat Mavic momenteel een ingrijpende transformatie doormaakt en er worden de komende maanden nog veel veranderingen verwacht. Als er in de tussentijd iets is waar Mavic op kan bouwen, is het wel zijn expertise. En wat is er beter dan zelf een carbon wiel te fabriceren om dat beter te begrijpen?
Carbon: van rol tot velg
Het merendeel van de wielen wordt elders vervaardigd (de carbon exemplaren in Roemenië, de aluminium wielen in Saint-Triviers-sur-Moignans), maar het hoofdkantoor van Mavic in Annecy behield wel een kleine productie-eenheid waar prototypes en limited editions het levenslicht zien. Ook de wielen voor de atleten die door het merk worden gesponsord en twee zeer hoogwaardige wegmodellen, de Cosmic Ultimate T en Cosmic Ultimate T Disc, worden hier gemaakt.
We trekken naar een ander gebouw en stappen de werkplaats binnen waar in een grote ruimte met gigantische tafels de koolstofvellen worden gesneden of gepositioneerd. Claude Righini, productmanager van de carbon wielen, zal ons er begeleiden bij het fabriceren van een velg.
In afwachting van onze komst, heeft hij de verschillende koolstofonderdelen (honderd per wiel) waarmee de velg wordt opgebouwd al voorbereid. Mavic ontvangt dit waardevolle materiaal in grote rollen die reeds geïmpregneerd zijn (de koolstofvellen zijn al met hars bedekt). Deze vellen worden vervolgens in zeer specifieke vormen gesneden om de verschillende delen te creëren die de velg zullen vormen.
Als deze onderdelen klaar zijn, gaan we verder met de eerste constructiefase: het maken van de velgstructuur die we aan de buitenkant zien. Op de nieuwe Mavic-wielen hebben de onderdelen de vorm van trapeziums om een mooie afwisseling in de oriëntatie van de vezels op het eindproduct te creëren. Hun positionering is relatief eenvoudig maar alles snel en goed doen, is een ander verhaal. We verwijderen aan één kant de beschermfolie, plaatsen het deel in de mal, duwen het goed plat en verwijderen de tweede beschermfolie. Dan nemen we een volgend deel en beginnen we van voor af aan, maar dit keer leggen we de koolstofvezels in de tegenovergestelde richting om afwisseling te creëren.
Deze koolstofvellen zijn gemaakt van unidirectionele vezels, een vorm van carbon die betere mechanische eigenschappen heeft dan geweven koolstof, waardoor er minder materiaal moet worden gebruikt voor hetzelfde resultaat en het eindresultaat dus lichter is.
Het nadeel is dat unidirectionele vezels gemakkelijker kunnen delamineren, met name ter hoogte van de gaten voor het ventiel en de spaken. Mavic gebruikte in het verleden een geweven versteviging rondom de velg, maar op nieuwere wielen is dat anders. Elke velgwand is voorzien van een glasvezelversterking en op de plaatsen waar de spaaknippels rusten, worden aan elk spaakgat kleine geweven koolstof inzetstukken geplaatst. Het voordeel van dit proces is dat het gewicht bespaart: ongeveer 70 gram per velg, simpelweg door de overtollige verstevigingen te verwijderen.
Fotograferen was hier uit den boze, want Mavic gebruikt zijn eigen techniek en gereedschap om de verstevigingen op zijn plaats te zetten en wil niet gekopieerd worden. Idem voor de bewerking waarbij men de structuur die we zojuist hebben gefabriceerd en het ‘bovenste’ deel van de velg – dat wil zeggen de basis waar het ventiel op rust en een stuk van de zijwanden aan de binnenzijde – met elkaar verbindt.
Zodra dit alles met elkaar is verbonden en dankzij de mal de vorm van een wiel heeft aangenomen, gaat het richting de persmachine. Dit keer zijn foto’s toegestaan, maar niet van te dichtbij omdat het merk het precieze proces geheim houdt. Het enige wat we weten, is dat men verschillende fasen bij verschillende temperaturen doorloopt en dat het vrij snel gaat. We hadden amper tijd voor een rondleiding in dit deel van het gebouw of onze velg was al klaar. Carbon ‘bakken’ is als brood bakken: het is niet gemakkelijk, het vraagt om ervaring, het gaat met vallen en opstaan en bovenal houdt iedereen zijn recept angstvallig geheim.
De laatste details
De laatste fabricagestap die we vandaag te zien krijgen, is de afwerking. Geen lak, verf of iets dergelijks op deze velgen, het carbon blijft zoals het is. Wel moeten we nog de overtollige hars afkuisen en de interne blaas verwijderen. Deze blaas zit in de velg en zorgt ervoor dat het koolstof goed tegen de randen van de mal wordt gedrukt tijdens het persen. Naderhand wordt de blaas via het ventielgat verwijderd. Deze manier van werken bespaart wederom gewicht. Bij eenvoudigere velgen blijft deze blaas waar ze zit. Praktisch verandert er niets: tussen de grote persdruk en het vacuüm trekken om de blaas te verwijderen, is de blaas onderhevig aan sterke mishandelingen. De blaas wordt dus maar eenmalig gebruikt omdat Mavic niet het risico kan lopen om deze te hergebruiken, elk gaatje kan immers rampzalige gevolgen hebben.
Het schoonmaken van de velg duurt bij ons MTB-wiel slechts enkele tientallen seconden, bij andere complexere producten kan het wel veel langer duren. Bij de Cosmic Ultimate T-wielen die we eerder al aanhaalden en die volledig uit carbon bestaan (naaf, spaken en velg), duurt dit bijvoorbeeld tussen de 2 en 8 uur per wiel. Ook al omdat alles manueel gebeurt.
Nu is het tijd om de gaten te boren voor de spaken, het aanbrengen van de decals en de montage om een afgewerkt Crossmax SL Ultimate-wiel te bekomen. Mavic mag dan wel tot de merken behoren die in serie produceren, toch is het verrassend hoeveel er hier nog manueel gebeurt. Soms lijkt het verschil met artisanale wielbouwers zelfs miniem. Zo wordt de spaakspanning op elk geproduceerd wiel met de hand gecontroleerd en afgesteld, of het nu gaat om een aluminium wiel dat in Saint-Triviers werd gevlochten of om een carbon exemplaar dat in Roemenië werd gespaakt.
Een korte omweg door de machinewerkplaats stelt ons in staat om snel de verschillende stadia van het vervaardigen van een naaf te begrijpen, beginnend bij een stuk aluminium dat een paar honderd gram weegt.
Het wiel mag dan wel klaar zijn, dat betekent niet dat het al op de markt wordt gebracht. Het is logisch dat een prototype naar het labo wordt gestuurd voor de nodige kwaliteitstests, maar het gebeurt ook dat men een wiel uit de productie loot en naar datzelfde labo stuurt.
Michel Lethenet vertrouwt ons toe dat Mavic hier het laatste anderhalf jaar heel veel aandacht aan besteed om terug recht te krabbelen en geeft toe dat er in het verleden wel eens te licht werd mee omgesprongen en men te veel vertrouwen had in het eindproduct. Vandaag voert men maar liefst 50 tests uit op elk wiel dat het labo binnenkomt.
Een serie tests
Kwaliteitsmanager Jean-Luc Veux legt ons uit dat vijf van zijn metingen bedoeld zijn om de normen te valideren, de rest zijn aanvullende metingen: statische metingen, vermoeiing, impact tests, … Dit gaat zelfs zo ver dat men met een elektronische microscoop het lichaam van het vrijwiel onderzoekt om de slijtage te bestuderen van de tanden.
We maken van de gelegenheid gebruik om DE vraag te stellen in naam van iedereen die reeds al de moeite van de wereld heeft gehad om een nieuwe band op een wiel te monteren: voert Mavic dit soort tests uit met verschillende bandenmerken? Goed nieuws, het antwoord is ja! Maar er wordt ons ook verteld dat ze al hebben gemerkt dat sommige merken moeilijker te monteren zijn dan andere, met soms eerder lagere toleranties die weinig manoeuvreerruimte overlaten aan de wielenbouwers.
Het is niet altijd even gemakkelijk om de invloeden van het terrein in het laboratorium na te bootsen en alle ervaring van het merk is dan ook nodig om de meest representatieve tests mogelijk te maken. Sommige testapparatuur (voor duurtests) is zo uniek dat ze nog angstvalliger beschermd worden tegen jaloerse en nieuwsgierige blikken dan prototypes van wielen. Het laboratorium alleen is echter niet voldoende om een nieuw product goed te testen en zoals elk merk heeft Mavic een heel team om zijn wielen in het terrein op de proef te stellen.
Dat team bestaat uit de ambassadeurs van het merk: renners die bij teams rijden die door het merk gesponsord worden (KMC-Orbea van Milan Vader bijvoorbeeld) maar ook de ingenieurs zelf, want een groot deel van het personeel van Mavic rijdt met de fiets. Onze dag eindigt trouwens met een ritje rond Annecy in het gezelschap van Michel Lethenet en Esteban Deronzier, de productiechef MTB. Een perfect moment om het werk en de zorgen even te vergeten en ons vol passie over te geven aan de sport waar we zoveel van houden …
Zelf een carbon velg fabriceren doe je niet elke dag. Wat we naast deze ongelooflijke ervaring onthouden, is dat we bij Mavic mensen hebben leren kennen die gepassioneerd bezig zijn met hun vak en de nodige kennis hebben om innoverende nieuwigheden uit hun hoed te toveren. Wanneer we de faciliteiten die een groot bedrijf waardig zijn, vooral in het testlaboratorium, buiten beschouwing laten, hadden we na ons bezoek het gevoel dat we in een jonge middelgrote onderneming waren aanbeland dat graag nieuwe dingen ontdekt en nog niet goed met zijn succes weet om te gaan.
Dit laatste heeft het voorbije decennium een zekere kloof gecreëerd met de verwachtingen van de markt en de consument, en na afloop maakten we de bedenking dat dit vooral kwam door een te grote wens om het goed te doen en oplossingen te bieden. In die mate dat men de geldende ‘standaarden’ en andere min of meer algemeen aanvaarde technieken begon te negeren. Dat loopt niet altijd goed af, maar de dag van vandaag werkt Mavic hard aan een wederopbouw en we hopen dat het leert uit de lessen van deze paar moeilijke jaren om opnieuw een toonaangevend merk te worden dat in staat is om intelligent te jongleren tussen innovatie, prestaties, betaalbaarheid en verwachtingen van gebruikers.
Meer info via www.mavic.com